Navigating regulation for export success
It’s important to recognise upfront that securing regulatory approval when selling a product abroad is a complex and sometimes lengthy process that requires expert support.
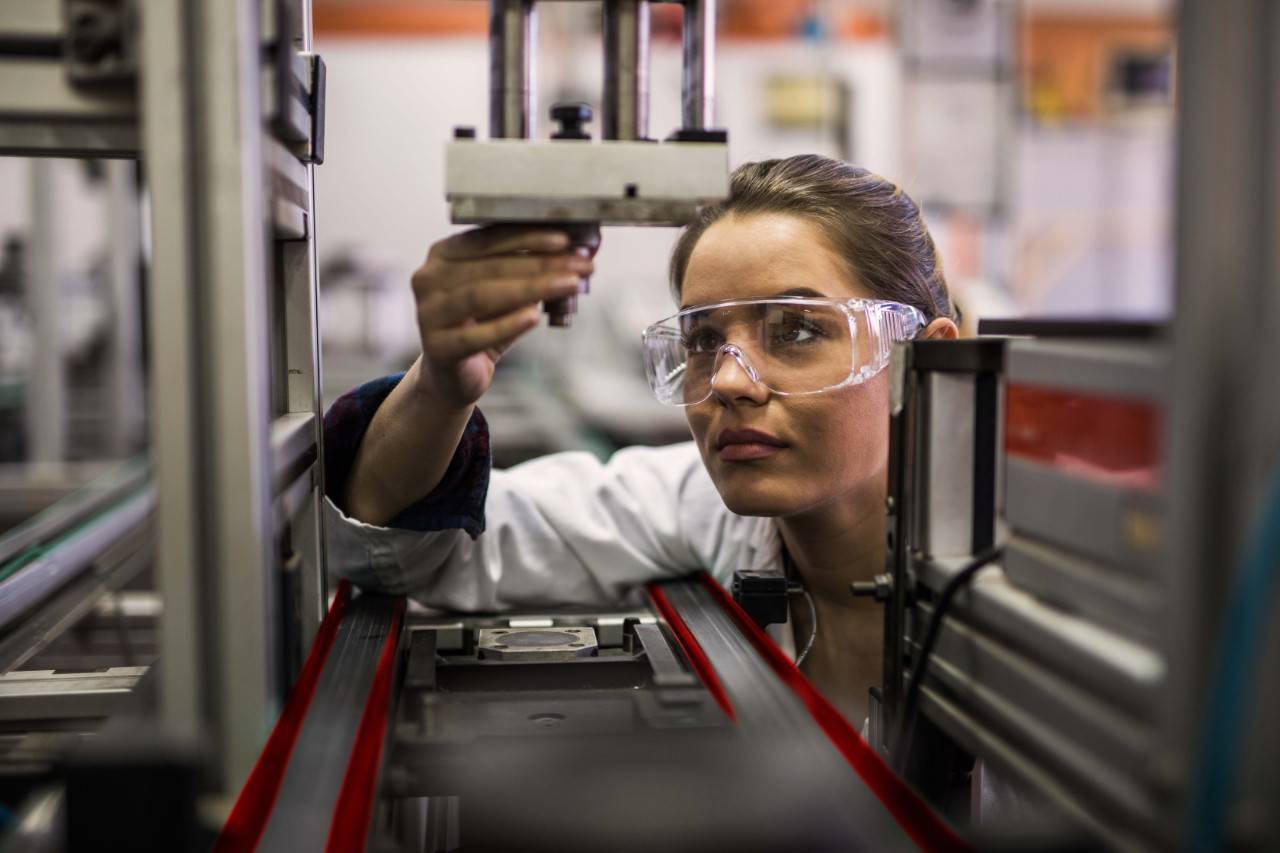
Larger companies employ in-house staff to manage this work, while smaller companies tend to make use of specialist consultants. The process is mainly digital.
Excluding medicines, most healthcare products are considered to be medical devices. Some 38 million Britons have contact with a medical device every day and there are more than 80,000 different devices on the UK market. All but the very lowest risk devices must conform to specific European Union (EU) directives.
These include the Medical Devices Directive (MDD), which defines a medical device as any instrument, apparatus, appliance, software, material or other article used alone or combined for humans to:
- diagnose, prevent, monitor, treat or alleviate disease
- diagnose, monitor, treat, alleviate or compensate for an injury or handicap
- investigate, replace or modify the anatomy or a physiological process
- control conception.
The MDD dictates that a medical device doesn’t achieve its main intended action by pharmacological, immunological or metabolic means, although it can be assisted by these. Products must meet the interests of patient safety, so they’re required to gain regulatory approval before they can be sold. They’re classified as:
- active implantable medical devices – including pacemakers and orthopaedic implants
- in vitro diagnostic products – including hepatitis or HIV tests, clinical chemistry, coagulation test systems, urine test strips, pregnancy tests and blood sugar monitoring systems for diabetics
- ‘general’ medical devices – the category into which the great majority of products fall.
In addition, medical devices are grouped into four different classes, ranging from Class 1 (general products) including the lowest risk devices, through to Class III for those that are considered most risky. The assessment process is more demanding for the higher risk classes – more detail here
In addition, UK products currently need to meet the CE requirements, which allow them to be sold throughout the European Economic Community (EEC). An announcement last week confirmed that CE marking will continue to be used and recognised in Great Britain until 30 June 2023, though a new route to market and product marketing will be available to manufacturers placing devices on the Great Britain market after 1 January 2021.
From 1 July 2023, all device manufacturers will need to meet the requirements for placing a UK Conformity Assessed (UKCA) mark on their products in Great Britain (more details here). Slightly different arrangements will apply in Northern Ireland (see here).
The Association of British HealthTech Industries is currently working through guidance with the Medicines and Healthcare products Regulatory Agency. It plans to host a virtual briefing for members in the coming weeks.
For exporters focused on non-EEC countries, a list of regulatory bodies around the world is available here. Approval times and costs vary enormously between countries, so it’s vital these are fully understood and built into export plans.
In next week’s briefing, we’ll discuss how to protect intellectual property.
Manufacturing sector news
August’s Manufacturing Purchasing Managers Index, published on 1 September, registered a figure of 55.2, indicating that manufacturing activity in the UK is rising at its fastest pace in six years. However, this was from a low base and was actually slightly lower than anticipated. The broader market context remains that job cuts are likely as the Government continues to unwind the Job Retention Scheme (JRS).
Still, new research from MakeUK does give reason to be positive. A third (31%) of manufacturers currently have no staff furloughed, its latest Manufacturing Monitor reveals, while more than half (54%) now think it will take less than 12 months to get back to normal trading conditions.
However, the research also shows that 62% of firms think the JRS should be extended for critical sub-sectors. MakeUK itself argues this is crucial to support the UK’s strategic industries, which are otherwise at risk of losing key skills and falling behind international competitors. Almost a quarter (23%) of firms disagree with the Government’s determination to close the scheme and 17% think it should be extended for all businesses. Significant numbers also say the scheme should be reintroduced in the event of another lockdown, and that we now need a new scheme to replace the JRS.
MakeUK points out that similar schemes in Belgium and Germany have already been extended, to the end of 2020 and 2021 respectively, while the Australian Government is extending its JobKeeper Payment scheme until March. In France, a new long-term short-time work scheme in specific sectors is planned for sectors where companies will suffer enduring loss of business from the pandemic.
The aerospace and automotive sectors are especially in need of an extension to the JRS, MakeUK says, given their position at the cutting edge of technology, which is likely to be vital to growth in the future. The organisation points to official data showing these two industries are the UK’s largest investors in research and development, accounting for more than two-thirds of such spending. The sectors are also among the hardest hit by coronavirus, with many job losses already announced and output predicted to fall by 33% (a £4.6bn loss in value) and 14% (£1.3bn) in automotive and aerospace respectively.
Across manufacturing as a whole, meanwhile, reshoring now looks to be an increasingly important agenda item. Bloxwich-based manufacturer, Albert Jagger Engineering, is one business proving what might be possible. It has worked with catapult centre, MTC, to bring the production of almost 250,000 fastening components back to the UK, achieving savings of 20%-30% in the process. The efficiencies come from a new factory layout, the introduction of new technology, retraining and a 50% decrease in stockholding costs.
Finally, on 10 September, Santander and MakeUK published the latest manufacturing sector fact card, providing a crucial update on the importance of the industry to the UK economy. The fact card include data ranging from export statistics to employment figures. We’ll look at the figures in more detail in our next briefing.
To discuss how Santander can help your business please contact: ccbsectorinsights@santander.co.uk